Our robots
Scroll down to read more

Voltaris 0.5 runs on the strafer chassis, using gripforce mecanum wheels for omni-directional movement. Since the major purpose of the robot was to test out the chassis and wheels, we use a simple robot that has an attachment to lower or lift up a grabber. This grabber can open and close to pick up objects like cones or 2024's FTC Sample element. Due the plain design we could easily code and test it..
Voltaris 0.5
Strafer Chassis
The strafer chassis is a popular drivetrain in the FIRST Tech Challenge, known for its exceptional maneuverability. It is the most easy to build chassis and is most team's first chassis, as it is also very light. Its modular design supports easy customization, enabling teams to adjust dimensions and add attachments.

Grabber
The grabber was mounted at the end of 2 long metal plates connected in the middle, to form an H shape. The servo for the grabber was mounted on top of it, and te grabber itself was 3D printed. It also had rubber bands around it to provide better grip for the grabber. In this bot, the slider had no ability to extend or retract and could only move 90 degrees up and down.

Voltaris 1.0 runs on the strafer chassis, using gripforce mecanum wheels for omni-directional movement. The sliders were made using Mizumi sliders and 3D printed brackets to join them together. Our grabber is a negative 3D printed replica of a sample to perfectly pick them up.
Voltaris 1.0
Strafer Chassis
The strafer chassis is a popular drivetrain in the FIRST Tech Challenge, known for its exceptional maneuverability. It is the most easy to build chassis and is most team's first chassis, as it is also very light. Its modular design supports easy customization, enabling teams to adjust dimensions and add attachments.

Grabber
Our first iteration grabber used a simple u-channel as the servo mount and a 3D printed gear box to make it easy to sontrol the grabber. It used one servo to open and close the grabber and one for a turntable. The grabber itself is completely 3D printed to be a negative replica of the sample.
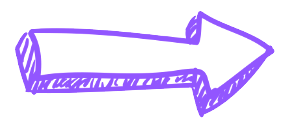
4 stage slider
The 4 stage slider is a key part of our robot, as it moves the grabber forward, backward, up and down to pick and place various elements. It is made using Mizumi sliders as they are very smooth and 3D printed brackets to join them together. They are also cascading which make them quite fast to extend or retract fully. The threading used in the slider also helps in keeping its tension and moving it.

Voltaris 2.0 also runs strafer chassis, using gripforce mecanum wheels for omni-directional movement. The sliders were made using Mizumi sliders and 3D printed brackets to join them together. Our grabber is a negative 3D printed replica of a sample to perfectly pick them up. The bucket is a simple bucket found lying around that is able to fit a sample in it.
Voltaris 2.0
Strafer Chassis
The strafer chassis is a popular drivetrain in the FIRST Tech Challenge, known for its exceptional maneuverability. It is the most easy to build chassis and is most team's first chassis, as it is also very light. Its modular design supports easy customization, enabling teams to adjust dimensions and add attachments.

Grabber
Our second iteration of the grabber was more custom as the whole gearbox was completely 3D printed and even the servo mount was 3D printed. As always, the claws were negative replicas of the sample to easily pick them up and transfer them into the bucket. It utilized one servo for opening and closing, one for turntable, and one to turn up and down to transfer it.

4 stage slider and 2 stage slider
The 4 stage slider has the bucket on it and drops the sample from the bucket to the high basket. The 2 stage slider in the front is to extend the grabber to grab samples from inside the submersible. Both sliders are made using Mizumi sliders and 3D printed brackets to connect them together. They are also cascading which make them quite fast to extend or retract fully. The threading used in the slider also helps in keeping its tension and moving it.
Bucket
The bucket mechanism is just a bucket on a long metal shaft. This bucket was attached to the top of the back slider and was able to swivel to drop the sample in the basket or be in the position to take it from the grabber.